
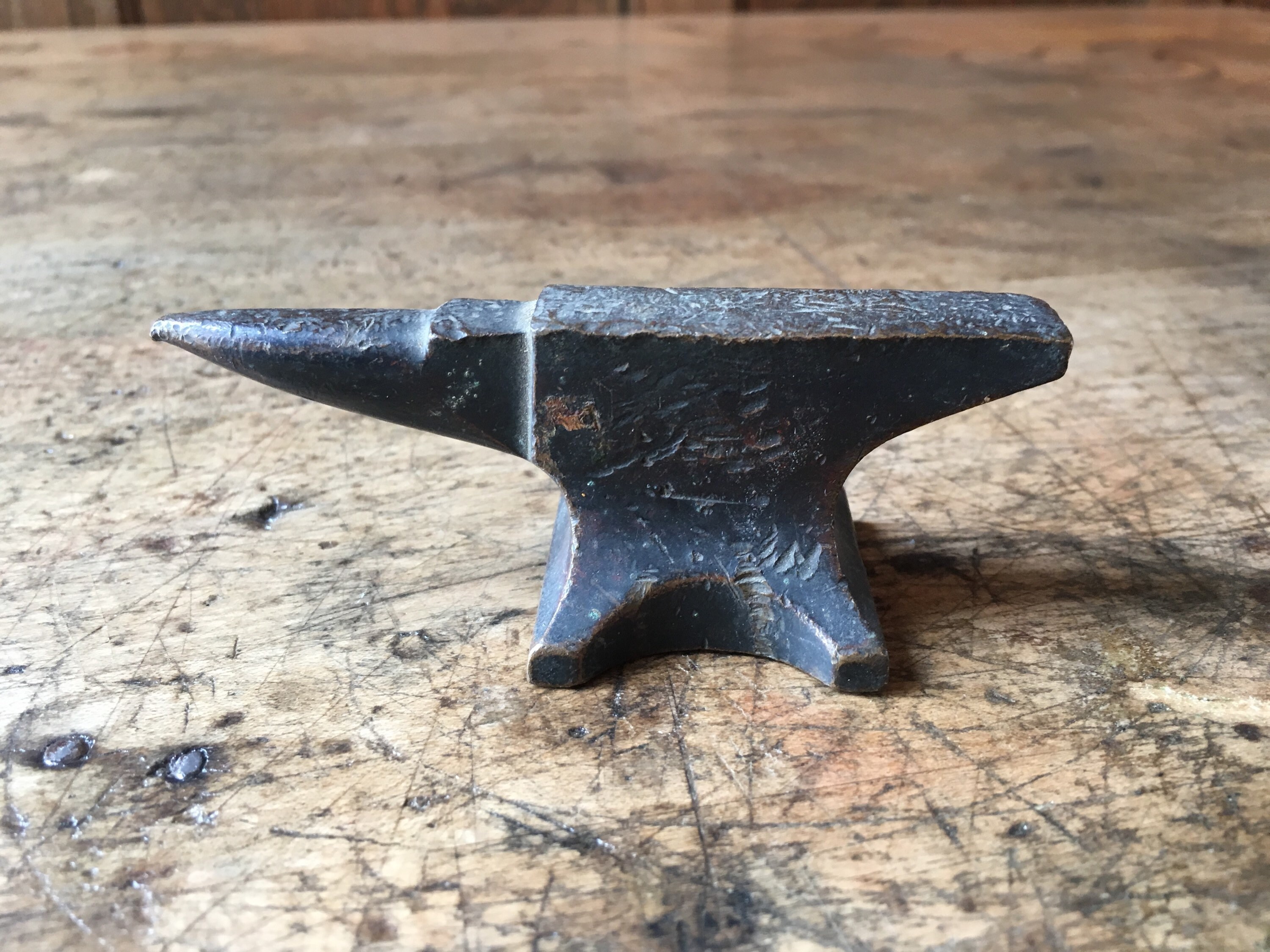
Keep in mind that is project is designed for someone with access to machine tools. The bottom anvil is a curved bearing from a pillow block, these are perfect for this application because they are hardened and also run perfectly smooth and straight even if they are mounted off-center.Ī bit about tools: Without welding, a mill or lathe, this project will be every difficult. A gigantic bearing would suffice, if you can find/get one. I didn't have the material or lathe capability to make a 8" diameter disk for use as the top anvil, so I recommend purchasing one online or at Harbor Freight. The screw in red is just to show how it passes up through the bottom to allow adjustment.
Cheap small anvil pdf#
I uploaded it as a PDF because the numbers and details are invisible as an image. The PDF attached to this step is the design for the overall machine, showing the main lengths and their arrangement. The ones not shown are just simple cut lengths of a standard size material (square tube, rod, etc) so a 2D drawing wouldn't be of any more help than just a written length. I've made drawings of all the complex parts for the project. The two wheels run against each other and the material is worked between them, with weight from the top one pressing down and pressure applied by the screw mechanism pressing the bottom one up, the sheet metal between is slowly thinned and curved. The only thing that changes is the size of the "C" shape body, and the length of the adjustment screw, to accommodate larger work pieces. You can scale the design ideas to make a benchtop model or a larger floorstanding version.
Cheap small anvil how to#
This instructable will be a rough-over of how to do most of the work, highlighting some insights I picked up along the way. You can see the results of my first test sheet, and all I had to go by was what I picked up from a couple of videos I saw on Youtube. Rolling in different directions and angled results in different effects. This stretching results in the material developing a curvature after many repeated passes. It works by stretching the small strip of material that comes in contact with both wheels as it is passed repeatedly between them. The whole process only took two weeks, start to finish. I read up on the theory of operation to get an idea of how it worked, looked at some pictures of wheels on the internet, and I set forth to design and build it. It is also very useful for planishing smoothing dimpled or bumpy sheet metal after hammering.Īn english wheel seemed like an excellent tool to build. Its used for making aircraft skins, car body parts, suits of armor and other applications where a smooth surface on the sheet is desired, something extremely difficult to achieve with a hammer. An english wheel is a classic hand-powered shop tool for making two-dimensional curves in sheet metal.
